Global construction productivity still stagnant, while the solution is at hand - expert
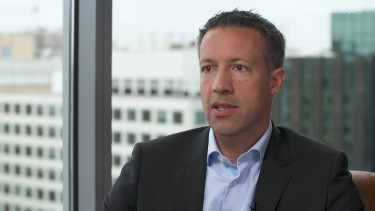
While EU reports often focus on sustainability in construction, they rarely address competitiveness. How do you think the construction sector can become more competitive?
Competitiveness in construction can be seen from different perspectives.
It’s not just about being able to compete globally, which is still limited in this sector, but it also involves boosting productivity—a key driver of competitiveness.
Historically, construction productivity has remained stagnant, particularly in Europe and the US, unlike other industries where productivity has risen steadily over decades. If you look at the data,
this stagnation becomes striking over a span of 10, 20, or 50 years.
Even small annual increases in productivity compound to make an enormous difference. In contrast, construction has flatlined, which creates significant opportunities for improvement.
It sometimes feels like the construction industry has reached a plateau—pouring concrete into different shapes seems to sum it up. How do you see modernization reshaping the sector?
The core construction process hasn’t changed much. While there have been notable innovations in materials—such as triple-glazed windows replacing single-glazed ones—how structures are assembled remains remarkably traditional. You put up a crane, lay bricks or install prefab panels, insert windows, and so on. It’s essentially the same as decades ago.
If you compare this to other industries like automotive or aerospace, their productivity revolutions stemmed from adopting standardized designs and mass production. Instead of crafting one car or plane at a time, they produce millions with variations, allowing economies of scale, automation, and optimization. In construction, this shift towards productization and industrialization hasn’t yet taken hold. There’s huge potential if the sector moves in this direction.
In Eastern Europe, we once relied heavily on prefabricated housing, assembling prebuilt elements to construct buildings quickly. However, this approach seems to have fallen out of favor. Was it abandoned because it wasn’t cost-effective?
Prefabrication was actually very efficient and cost-effective. It played a crucial role in post-war reconstruction, enabling rapid rebuilding.However, the criticism often revolved around aesthetics and perceived quality of living.
While I understand those concerns, modern modular construction has evolved significantly.
Today’s techniques allow for a high degree of customization and superior building standards, both in functionality and design.
This isn’t just about replicating the old prefab model but taking it several steps further—producing entire rooms or even larger modules offsite, fully equipped and ready to be assembled quickly on-site.
Many reports on construction, such as the EU's sustainability-focused studies, emphasize "innovation" repeatedly but rarely specify how to innovate. Can construction adopt revolutionary changes similar to those in fields like pharmaceuticals or artificial intelligence?
Absolutely, although the construction industry starts from a much lower base in terms of innovation and R&D spending. It is one of the least digitized sectors—when we last measured, it was even less digitized than agriculture.
Digitalization can unlock significant productivity gains. For example, building information modeling (BIM) allows developers to design projects digitally with incredible precision. Instead of creating detailed architectural drawings and resolving engineering issues on-site, BIM enables virtual assembly, error detection, and precise planning before construction even begins.
When paired with modular production, this could revolutionize construction logistics, reducing errors and inefficiencies.
Is the lack of competitiveness and innovation in construction a global issue, or is it more specific to Europe and the US?
It’s a mix. Europe and the US have historically been more productive in construction due to higher use of machinery and better organization, but productivity has flatlined for decades. In emerging markets, construction productivity is improving, but often from a very low baseline.
Japan offers an interesting case. They’ve industrialized construction significantly, driven by their need for earthquake-resistant buildings.
In Saudi Arabia, they’re leveraging industrialized techniques for large-scale projects like NEOM. Similarly, countries like the UK, Australia, and Singapore are experimenting with modular and 3D volumetric construction, though challenges remain in scaling these approaches effectively.
Statistical data on innovation investment in construction is hard to come by. Most figures seem to track only the cost of building houses. How much is actually invested in competitiveness and productivity in this sector?
That’s a challenge. Most construction investment data captures capital spent on equipment or real estate, but actual R&D investment is very low. Many construction CEOs adopt a “capital-light” strategy, minimizing fixed assets to remain flexible in this highly cyclical industry.
Ironically, if you consider the engineering costs for individual projects, you could argue that 20% of construction spending is essentially R&D—but it’s fragmented and project-specific. If we pooled these resources to develop standardized designs and modular systems, it could transform the industry.
Ten or fifteen years ago, there was a lot of excitement around 3D printing in construction. Has it lived up to the hype?
3D printing has its place in construction, particularly for customization, but it’s not inherently a cheap or efficient technology. For large-scale productivity improvements, other approaches—like industrialization and modular construction—are more promising.
While 3D printing may complement these efforts, it’s unlikely to become the dominant method anytime soon.
Cover photo: Mckinsey Global Institute
A cikk elkészítésében a magyar nyelvre optimalizált Alrite online diktáló és videó feliratozó alkalmazás támogatta a munkánkat.